「刃物交換の手間を減らしたい…」
「加工不良を減らして納期を守りたい…」
金属切削加工の現場では、刃物欠損や加工不良といった切削トラブルがつきもの。これらのトラブルは、作業効率の低下や不良品の増加に繋がり、頭を悩ませている方も多いのではないでしょうか?
特に、初心者の方やこれから経験を積む中堅の作業員の方にとっては、適切な対処法を学ぶことが重要です。
本記事では、刃物欠損のよくある原因を3つのステップで分析し、それぞれの原因に応じた具体的な対策を紹介します。
図解や事例を交えながら解説していくので、この記事を読めば、明日から現場ですぐに使えるノウハウが身につきます。切削トラブルを未然に防ぎ、生産性向上とスキルアップを実現しましょう!。
切削トラブルを未然に防ぐ!刃物欠損の3大原因と対策
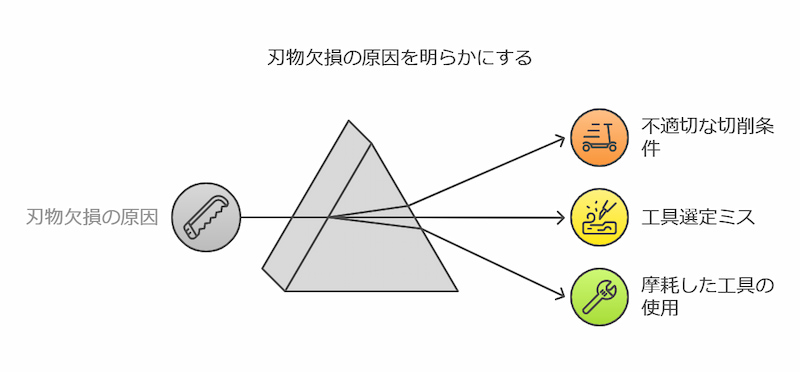
刃物欠損は、加工不良、生産性低下、工具費増加など、様々な問題を引き起こします。
主な原因としては、下記の4つが挙げられます。
- 不適切な切削条件
- 工具選定ミス
- 摩耗・破損した工具の使用
- 不適切な切粉処理
これらの原因を理解し、適切な対策を講じることで、刃物欠損を最小限に抑え、効率的かつ高精度な切削加工を実現できます。
刃物欠損のよくある原因【刃物欠損】【切削条件 最適化】
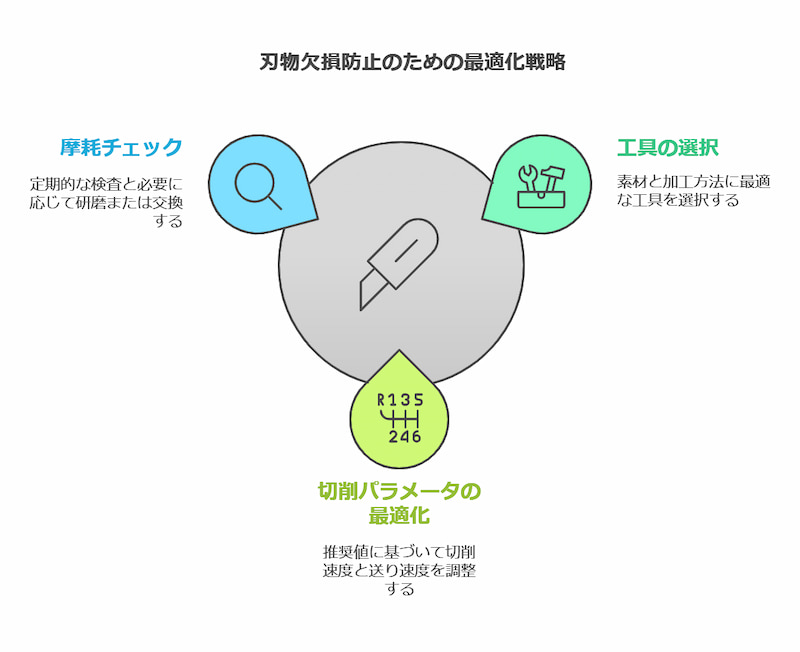
では、刃物欠損のよくある原因を具体的に見ていきましょう。
1. 不適切な切削条件
送り速度が速すぎる、切込みが深すぎる、切削速度が不適切などは刃物に過大な負荷をかけ、欠損の原因となります。
【具体的な例】
- 高速切削時の切削温度上昇: 切削抵抗の高い材料で高速切削を行うと、刃先温度が上昇し、工具摩耗を早め、欠損しやすくなります。
- 送り速度と切込み量のアンバランス: 送り速度に対して切込み量が大きすぎると、工具にかかる負荷が増大し、欠損のリスクが高まります。
- 切削速度と被削材の硬さの不適合: 切削速度が被削材の硬さに対して適切でない場合、工具寿命の低下や欠損に繋がります。
2. 工具選定ミス
加工対象物に適さない材質や形状の工具を使用すると、摩耗や欠損が早まります。
【具体的な例】
- 高硬度材への不適切な工具選定: 高硬度材に、炭素鋼工具を使用すると、耐摩耗性が低いため、すぐに刃先が摩耗してしまいます。
- 被削材の形状に合っていない工具の使用: 溝加工に適していない形状の工具を使用すると、工具の側面がワークに接触し、欠損の原因になります。
3. 摩耗・破損した工具の使用
摩耗や欠損した工具をそのまま使用すると、加工精度が悪化し、さらに大きな欠損につながる可能性があります。また、びびり振動が発生しやすくなり、加工面が荒れる原因にもなります。
【具体的な例】
- 摩耗した工具の使用による加工面荒れ: 刃先が摩耗した工具を使用し続けると、切削抵抗が増加し、加工面に傷やバリが発生しやすくなります。
- 欠損した工具の使用による加工不良: 欠損した工具を使用すると、寸法精度不良や表面粗さの悪化など、重大な加工不良に繋がることがあります。
4. 不適切な切粉処理【切りくず処理】
切粉が刃物に絡まったり、加工面に詰まったりすると、切削抵抗が増加し、刃物欠損や加工不良を引き起こす可能性があります。
【具体的な例】
- 切り屑の溶着: 高温で発生した切り屑が工具に溶着すると、切れ味が悪くなり、刃先が欠損しやすくなります。
- 切り屑詰まりによるトラブル: 切り屑が適切に排出されずに加工面に詰まると、工具の逃げ場がなくなり、欠損や破損に繋がります。
刃物欠損が引き起こす損失【刃物欠損】
刃物欠損は、以下のような様々な損失に繋がります。
- 生産性低下: 刃物欠損による工具交換や再設定に時間がかかり、生産性が低下します。
- 例:1回の工具交換に15分かかると、1日8時間稼働で30分以上のロスが発生する可能性があります。
- 加工精度不良: 欠損した刃物で加工を行うと、寸法精度や表面粗さが悪化し、不良品が発生するリスクが高まります。
- 例:欠損した工具を使用することで、±0.1mmの寸法公差を満たせない製品が発生する可能性があります。
- 工具費の増加: 刃物欠損の頻度が高いと、工具の交換頻度も上がり、工具費が増加します。
- 例:1本1万円の工具を月に10本交換すると、年間120万円の工具費がかかります。
- 安全性の低下: 刃物欠損は、切削中の破片の飛散など、作業者の安全を脅かす可能性があります。
- 例:高速で回転する工具が破損すると、破片が作業者に当たり、怪我を負わせてしまう可能性があります。
刃物欠損を防ぐための3つの対策【切削トラブル】【刃物欠損】
刃物欠損による様々な損失を最小限に抑えるために、以下の3つの対策を心がけましょう。
加工における工具選定は、使用する材料や加工方法に応じて最適な工具を選ぶことが重要です。以下に、最新の情報を基にしたマシニングで使用する場合の工具選定のポイントを整理しました。
1. 工具選定のポイント:素材と加工方法に最適な工具とは?
加工材料の硬度、被削材の形状、加工方法に適した工具材質、コーティング、形状を選択します。工具メーカーのカタログや技術資料を参考に、推奨される工具を選びましょう。
被削材 | 工具材質 | コーティング | 工具形状 |
---|---|---|---|
ステンレス鋼 | 超硬合金 | TiN, TiAlN | エンドミル、ドリル |
高硬度鋼 | CBN, ダイヤモンド | PCD | エンドミル、バイト |
アルミ合金 | 超硬合金, ダイヤモンド | DLC, TiAlN | エンドミル、リーマ |
【具体的な例】
- ステンレス鋼の加工には、耐熱性・耐摩耗性に優れた超硬合金製の工具が適しています。さらに、PVDコーティング(例えばTiNやTiAlN)を施すことで、耐摩耗性が向上し、工具寿命が延びます。これにより、加工時の熱発生を抑え、より高い加工精度を実現できます。
- 高硬度材の加工には、CBN工具やダイヤモンド工具が有効です。CBN工具は、高硬度鋼の高速加工に適しており、耐摩耗性が高いため、長時間の連続加工が可能です。ダイヤモンド工具は、鏡面加工などの高精度加工に適しており、特に非鉄金属や複合材料の加工において優れた性能を発揮します。
- アルミ合金の加工には、超硬合金やダイヤモンド工具が推奨されます。特に、ダイヤモンドコーティングを施した工具は、アルミニウムの加工において優れた潤滑性を提供し、切りくずの排出性を向上させます。また、DLC(ダイヤモンドライクカーボン)コーティングも、摩耗耐性を高めるために効果的です。
このように、被削材の特性に応じた工具選定を行うことで、加工効率や品質を大幅に向上させることが可能です。
2. 切削条件の最適化で刃物欠損を防止|初心者でもできる3ステップ

工具メーカーの推奨値を参考に、切削速度、送り速度、切込み量を最適化します。
- 推奨値の確認: まず、工具メーカーのカタログや技術資料で、使用する工具と被削材に推奨される切削条件を確認します。
- 試加工の実施: 推奨値を参考に、試加工を行いながら、切粉の形状や表面粗さを確認し、切削条件を調整します。
- 最適値の決定: 切粉がカール状に排出され、加工面が良好な状態になる切削条件を最適値として決定します。
【具体的な例】
- 切粉が粉状になる: 送り速度が遅すぎる、または切込み量が少なすぎる可能性があります。送り速度を上げたり、切込み量を増やしたりしてみましょう。
- 切粉が鳥の巣状になる: 送り速度が速すぎる、または切込み量が大きすぎる可能性があります。送り速度を下げたり、切込み量を減らしたりしてみましょう。
- 切粉がカール状になる: 切削条件が適切な状態です。この状態を保つように、切削条件を調整しましょう。
また、切削油剤の種類や量も重要です。加工材料と工具に適した切削油剤を使用し、適切な量を供給しましょう。
3. 定期点検で工具寿命を延ばす|メンテナンス方法を解説
工具の摩耗状態を定期的にチェックし、必要に応じて研磨または交換を行います。
【具体的な点検方法】
- 目視検査: 工具の刃先に目に見える欠損や摩耗がないか確認します。
- 顕微鏡による検査: 目視では確認できない微小な欠損や摩耗を拡大して確認します。
- 工具寿命管理ソフトの活用: 工具の使用時間や回数などのデータを記録し、摩耗状態を予測するソフトを活用するのも効果的です。
【工具の保管方法】
- 工具は、乾燥した場所で保管し、衝撃や振動を与えないようにしましょう。
- 工具同士が接触すると、刃先が欠損する恐れがあるので、専用の工具ホルダーを使用するのがおすすめです。
切削トラブル解決のための具体的な手順|トラブルシューティング完全ガイド
万が一、切削トラブルが発生した場合でも、落ち着いて以下の手順でトラブルシューティングを行いましょう。
- トラブル発生時の状況把握【切削トラブル】
- 発生したトラブルの内容を正確に把握します。
- 発生日時、加工対象物、使用工具、切削条件、トラブルの症状などを記録しましょう。
- トラブル発生時の状況を写真や動画で記録しておくと、原因究明に役立ちます。
- 原因の特定と解決策の実施【切削トラブル】【刃物欠損】
- 収集した情報に基づき、トラブルの原因を特定します。
- 原因に応じて適切な解決策を実施します。
- 例: 切削条件の調整、工具の交換、切粉処理方法の変更など。
- 再発防止策の実施【切削トラブル】
- トラブルの原因を分析し、再発防止策を検討します。
- 作業手順の見直し、教育の実施、設備の改善など、具体的な対策を講じましょう。
- 定期的な点検やメンテナンスを実施し、トラブルの発生を未然に防ぎます。
結論・まとめ
刃物欠損をはじめとする切削トラブルは、生産性低下や工具費の増加など、様々な損失につながります。しかし、適切な工具選定、最適な切削条件の設定、そして定期的な点検とメンテナンスを行うことで、これらのトラブルを大幅に削減することが可能です。
本記事で紹介したトラブルシューティングの手順を参考に、発生したトラブルの状況を正確に把握し、原因を特定、解決策を実行することで、再発防止にも繋がります。さらに、工具メーカーのカタログや技術資料を活用し、常に最新の切削技術を学ぶことで、更なるスキルアップを目指しましょう。